Prof. Dr. Taylan ALTAN
Adam GROSECLOSE, Prof. Dr. Taylan ALTAN
Bölüm 2
Test için en uygun yağla koşullarının belirlenmesi
Yazarın Notu: Bu makale 2 kısımdan oluşan ve Ohio State Üniversitesi Hassas Şekillendirme Merkezi’nde yağlayıcı performansını arttırmak için kullanılan pratik test yöntemlerini kritik eden yayının ikinci kısmını oluşturmaktadır.
Derin Çekme Çalıştayı’nda tartışılan en önemli konulardan biri Hassas Şekillendirme Merkezi (CPF)’nde gerçekleştirilen bir projeyle bağlantılı olan ‘Yağlama’ konusuydu. Bu proje kapsamında CPF, 19 farklı yağlayıcı ve bunların farklı malzemelerle olan performansını incelemeye başladı. Malzemeler arasında fosfatlama ön işlemi uygulanan ve uygulanmayan iki sınıf Galvaneal® çekme kalitesinde çelik ve bunun yanında alüminyum alaşımı sac yer alıyordu. Yağlama testi için 6 farklı firmadan farklı yağlayıcılar temin edildi.
Yağlayıcılar ayrı ayrı ve çeşitli kombinasyonlar şeklinde uygulandı. Hadde yağı, temizleme yağı ve derin çekme yağlayıcılarının kullanıldığı otuz dört farklı yağlama kombinasyonuna ön bir test uygulandı. Buradaki amaç test esnasında uygulanmak üzere en iyi iki ya da üç yağlama koşulunun belirlenmesi idi.
Değerlendirme Testleri
Yağlayıcılar aşağıdaki prosedürler eşliğinde değerlendirilmiştir.
Dayanım Testi – Bu test, her yağlayıcı kendi kombinasyonlarında kullanılarak ve bu karışımın dört hafta süresince bekletilmesi ile gerçekleştirilmiştir. Karışımın ne şekilde reaksiyon verdiği (çözünme ya da ayrışma) periyodik olarak incelenmiştir.
Temizlenebilirlik/Boyanabilirlik Testi – Bu testte yağlayıcı kombinasyonları test edilen sac malzemelere uygulanır ve şirketin depolama koşullarını simüle edebilmek için birkaç hafta boyunca bekletilir. Bu uygulamaya kimi zaman stack stain testi adı da verilir. Bekleme periyodunun ardından yağlayıcı giderilir. Yağlayıcının giderilme zorluğu ve sacın yüzeyinin görünüşü kaydedilir. 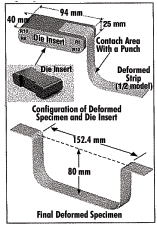
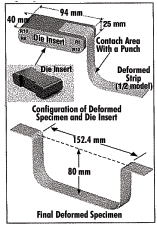
Strip Draw Testi (SDT) – Bu testte yağlayıcı, 14-in’e 1-in malzeme parçasını şapka şeklinde çekmek için kullanılmıştır. Örneğin çekme derinliği ve basma kuvveti kaydedilmiştir (Şekil 1).
Cup Drawing Testi (CDT) – Daha büyük bir çekme derinliği ve daha az basma kuvveti ile oluşturulan şekil daha iyi yağlayıcı performansı göstermiştir (Şekil 2).
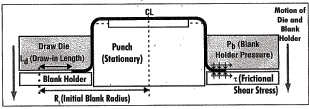
Test Sonuçları
Bu proje için dayanım testi, temizlenebilirlik testi ve ön SDT testleri yürütülmüş ve sonuçlar özetlenmiştir. Dayanım ve temizlenebilirlik/boyanabilirlik testleri yağlayıcı tedarikçileri tarafından OEM ve CPF ile işbirliği içerisinde gerçekleştirilmiş ve sonuçların analizinde tedarikçilerin bu alandaki tecrübelerinden de faydalanılmıştır. Bu iki test arasından CPF çalışmadaki 11 yağlayıcı koşulunun elenmesine olanak sağlamıştır. Ön SDT testleri OEM prosesi için testin ince ayarının yapılmasında kullanılmıştır. İdeal koşulların sağlanması için üretimdekine benzer baskı hızı kullanılmıştır. En yüksek baskı basıncının ve yağlayıcılar arasındaki en büyük değişimin elde edilmesi için baskı plakası kuvveti (BHF) maksimize edilmiş ve takım çapı minimize edilmiştir.
Malzeme/takım ara yüzeyinde en zorlu yağlama koşulları ve en yüksek basınçları verdiği için olası en küçük kalıp köşesi çapı seçildi. BHF sonlu eleman yöntemi (FEM) simülasyonları ve deneyleri baz alınarak kararlaştırıldı. Numuneler 5 ton altında kırılıyordu ve bunun yanında 3 ton ile 4 ton arasında uzama açısından çok fark göstermiyordu. Bu yüzden BHF olarak 4 ton seçildi (Şekil 3).
Baskı hızı, beklenildiği şekilde, uzama açısından önemli bir rol oynadı ancak bu değer bulunan genişliğe kadar değildi.
Optimum hız olarak belirlenen değer 40 mm/s idi ancak bu hız tüm BHF değerlerinde çatlaklara sebep oldu. 20 mm/s hız 4 ve 5 tonluk kuvvetlerde çatlaklara sebep olurken 3 tonluk kuvvette çok az bir değişime neden oldu. Diğer baskı hızları 4 ve 10 mm/s test edildi ve bu testler sonucunda çatlak içermeyen numuneler elde edildi. Bu yüzden, aynı zamanda üretim hızına da yakın olduğu için, 10 mm/s hızda karar kılındı.
Seçilen test parametreleri ile SDT’ler şu anda kalan 23 yağlama koşulunu analiz etmeye hazır durumda. SDT tarafından belirlenen en iyi yağlama koşulları, yağlayıcıların yüksek yüzey basıncı koşullarında performansının değerlendirilmesi için sonrasında Cup Drawing ve Ironing Testlerine tabi tutulacak (Şekil 4).
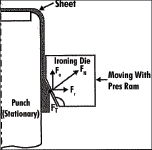