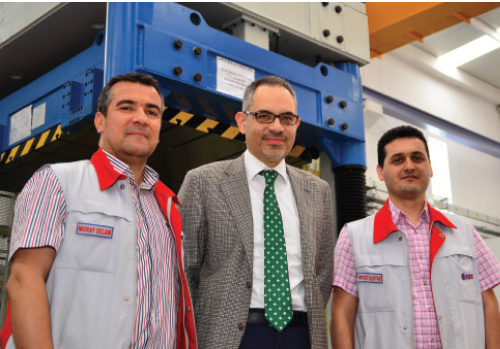
İsmim Murat Selam, Plast Met firmasında proje koordinatörlüğü görevini yürütüyorum. Firmamız 1987 yılında, İstanbul’da kuruldu. 2004 yılında da üretim yaptığımız Bursa fabrikamızı hizmete açarak, iki lokasyon da hizmet vermeye devam ediyor. İstanbul’da ilk olarak Ümraniye’de kalıp hane olarak faaliyete başladık. Daha sonra Dudullu OSB civarındaki bölgeye taşındı. Şu anda ise Tuzla’da faaliyetimize devam ediyoruz. İstanbul’daki mevcut yerimizde 4 bin 500 m2 kapalı alanda sadece kalıp hane bölümümüz çalışıyor. Daha önce Kalıphane içerisinde deneme amaçlı olarak bulunan enjeksiyon makinalarımız ise, yine Tuzla’da aynı sanayi sitesi içerisinde yer alan yeni açılan tesisimize transfer edildi. Böylece, İstanbul ve Bursa’da toplamda 3 tesisimizde, yaklaşık (110 personel İstanbul Kalıphanede) 450 personelimiz ile birlikte üretim yapıyoruz.
İstanbul’da hem üretim, hem de kalıp fabrikası bulunmakta. İstanbul’da; plastik enjeksiyon kalıpları, bi-enjeksiyon dediğimiz iki farklı renk bileşeni içeren kalıplar, progresif kalıplar yapabiliyoruz. Özellikle 15-20 adımlık, özel bağlantı taşıyıcı kalıp imalatını kendi üretimimiz için yapıyoruz. Bursa’da ise plastik parça, kablo üretimi ve bu mamullerin montajlanma işleri yapılmakta. İstanbul’da ayrıca, kendi müşterilerimiz için üretim; yakın gelecekte de montajlı parça teslimatı yapacağız.
Alıştırma Presi almaya ne zaman ve hangi düşünce ile karar verdiniz?
Aslında, alıştırma presi yatırımı konusunda uzun zamandır düşüncemiz vardı. Önceki lokasyonumuzda ikinci katta bulunmamızdan ötürü bu yatırımı gerçekleştirememiştik. Gerçi o zaman da ihtiyacımız vardı. Biliyorsunuz ki kalıp alıştırma presine sahip değilseniz, vinç altında ‘düşürerek kapama’ diye tabir edilen yöntemle yapılıyor. Bu da çevresinde büyük bir titreşime sebep oluyor ve etrafında bulunan makinaların hassasiyetini bozuyor. Ayrıca sağlıklı bir yöntem olmadığından ötürü, yapmaya çalıştığınız işlemi defalarca tekrar etmeniz gerekiyor. Bu da zaman ve iş kaybına sebep oluyor. Tüm bu olumsuzluklar neticesince, 2007 yılında ilk düşünmeye başladığımızda yer ve o dönemli global krizin de yaratmış olduğu problemlerden ötürü bu yatırımı gerçekleştiremedik. Bugün, Tuzla’da bulunan kalıp imalathanemizin zemin kat konumlu olmasının da avantajını kullanarak, alıştırma presi yatırımının mutlaka yapılması gerektiği kararında hem fikir olarak araştırmalara başladık.
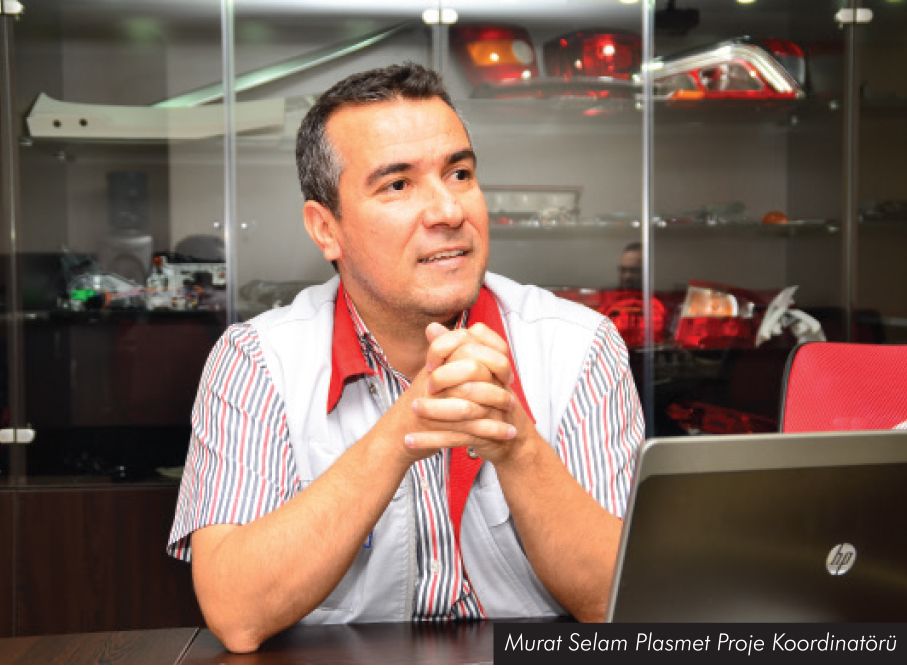
Tandem firmasını ve satışı yaptıkları MILLUTENSIL MIL-202’yi tercihiniz altında yatan sebepler nedir?
Uzun süren araştırmalarımız oldu açıkçası. Yurt dışında birçok firmaya da ziyaretler gerçekleştirdik. Bunun haricinde gerek ben (Murat Selam) gerekse Hayati Bey de birçok kalıphanede de görevler aldık. Geçmişten gelen tecrübeler ve piyasada bilinen en iyi makinelerden birisi olması, fonksiyonelliği, ayrıca ilave parça entegrasyonu (misal, biz verdiğimiz siparişe iki ilave hidrolik takviyesi yaptık) gibi avantajları bulunuyor. Ayrıca birlikte iş yaptığımız firmalarda ve gittiğimiz kalıpçılarda da MILLUTENSIL’i gördük; yaygın oluşu ve kullanım kolaylığı, Tandem ve MILLUTENSIL’i seçme sebeplerimiz arasında yer aldı ve referanslarını da kendi gözlerimizle gördüğümüz için ikinci bir marka arayışı içerisinde girmedik açıkçası.
Tabi yaygın servis ağı, herhangi bir arıza yaşanması durumunda hızlı cevap ve parça değişimi gerektiği anlarda en kısa sürede tedarik edilebiliyor olması da bizim için çok önemli hususlar arasında yer alıyordu. Tandem’i tercih etmemizin ardında yatan sebepler de bunlar oldu. Mesela, taşınma esnasında kendilerine ulaştığımızda en hızlı bir geri dönüş yaptılar ve şimdiye kadar herhangi bir sorun yaşamadık. İyi ki de MILLUTENSIL MIL-202’yi aldık, zira özellikle bu dönemde çok ciddi faydalarını gördük.
Örnek olarak verebileceğiniz; şu ebatlı kalıpta alıştırma presi olmadan x süre/maliyet, alıştırma presinde ise y süre/maliyet bilgisi paylaşabilir misiniz?
Daha önce yapmış olduğumuz tüm alıştırma sonuçlarını enjeksiyon üzerinde görüyorduk. Denemeyi her zaman kendi bünyeniz içerisinde yapamayabiliyorsunuz. Uzun yıllardır büyük kalıplarımızı Bursa’da deniyorduk, artık İstanbul’da da büyük ebatlı enjeksiyon makinamız bulunmakta. Bir kalıbı hazırlıyorsunuz, Bursa’ya naklini yapıyorsunuz, denemeyi alıyorsunuz ve hiç beklemediğiniz bir sonuçla karşılaşıyor, bir alanda çapak olduğunu görüyorsunuz. Ve o çapağın düzeltilebilmesi için kalıbın tekrar İstanbul’a geri nakledilmesi, gerekli düzeltmelerin yapılması ve sonucun yeniden görülebilmesi için bir kez daha Bursa’ya nakledilmesi gerekiyordu. Çok karmaşık kalıplarda 6 sefere kadar bu olayı yaşadık. Ancak MILLUTENSIL MIL-202 alıştırma presi sonrası, bu işlemler en fazla 2 sefer gerçekleşiyor. Çünkü alıştırma presi üzerinde tüm yüzeylerin birbirleriyle temas edip etmediğini görme şansını elde ediyorsunuz.
Şirket içerisinde bir talimat hazırladık konu ile ilgili olarak; “Alıştırma presine bağlanmayan hiçbir kalıp, Bursa’ya sevk edilemez” çünkü alıştırma presine bağlanmayan kalıplarda bir takım sıkıntılar oluyor. Şayet elinizde MILLUTENSIL gibi bir alıştırma tezgahı yoksa bunun yerine vinç veya araya parça sıkıştırıp, kalıbın diğer bölümünü düşürerek basınç uyguluyorsunuz. Aslında bu çok yanlış bir yöntem. Siz bu kalıbı işlediğiniz zaman mutlaka erozyon bölümünde stoplar, atlanmış bölgeler kalıyor. Ve bu alanlar plastiğin formunu oluşturan bölgeler oluyor. Bu bahsettiğimiz şekilde kontrolsüzce yukarıdan aşağıya güç uyguladığınız zaman alıştırma gereken yerlere güç uygulayarak kırıyorsunuz. Tabi bu yapılırken, kalıbın bir tarafının, diğerinden daha erken düşmesini sağlayarak aslında paralel kapanıp açılmasını hiçbir zaman yapmamış oluyorsunuz. Doğal olarak bu durum neticesinde çok iyi işlemiş olduğunuz yüzeyde deformasyonlar meydana gelmiş oluyor. Dolayısıyla oluşan handikaplar, daha sonrasında çok daha büyük işler olarak, olumsuz geri dönüyor. Şayet bu dengesiz bırakma neticesinde bir bölümde kırılma meydana gelirse, o bölgeye kaynak yapmanız gerekiyor. Hele ki bu parça desenli ise mutlaka müşteriye geri dönüş yapmanız gerekiyor.
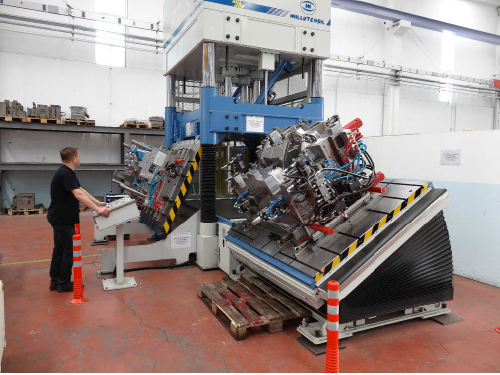
Böylece iş çok uzuyor. Bizim MILLUTENSIL’i almadan önce yaşadığımız en büyük sorunlardan bir tanesi bu olmuştu. Kalıp teknisyeni “alıştırmam bitti” diyerek enjeksiyona geçtiği zaman, parça üzerindeki çapakları görüp sadece bu bölgelere müdahale edip her seferinde deneme yanılma yöntemiyle kalıp düzeltiliyordu. Şimdi ise, imzalı prosedür haline getirdiğimiz alıştırma presine girmeden ve kontrol edilmeden, kalıp sevkiyatımız yapılmıyor artık. Ve böylece teknisyen de kalıbından emin olmuş oluyor. Kimi zamanlarda yaptığımız kontrollerde teknisyenler ilk başta buna muhalefet ediyorlardı. Çünkü bağlamak ve alıştırmaz zaman alıcı gibi görünüyor. Hele ki zor yüzeyler barındırmıyorsa, vinçle kapat-aç yapıldığında çok daha çabuk oluyormuş gibi geliyor. Fakat sonucu çok daha kötü oluyor. Artık bu ortadan kalktı. Emin olduğumuz yüzeylere sahip kalıplar haricinde; misal paralel, bir tarafı taşlanmış düz yüzeyleri kalıpların ölçümlerini de kendimiz yaptığımız için alıştırma presine ihtiyaç duymuyoruz. Ama karmaşık formlara sahip olan kalıplar mutlaka ve mutlaka alıştırma presine bağlanır, gerekli kontrolleri yapılır müdahale edilmesi gereken bir durum olursa, vakit kaybetmeden giderilir.
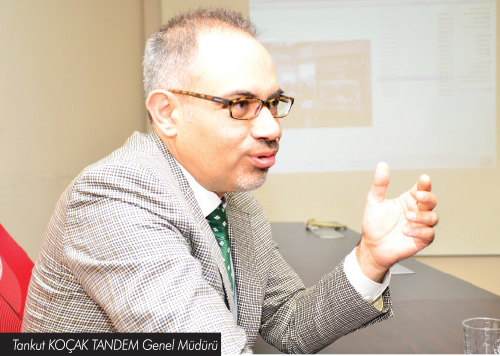
Tabi ki. Çoklu insert olan kalıplarımız var. Bu insert kalınlıkları 2mm’den başlayarak, çok daha büyük ebatlara ulaşabiliyor. Örneğin, genişliği 4-5 mm olup, boyu 10mm’lere varan bazı insertlerimiz var. Bu insertler, vinç altında darbeyle vurdurulduğu zaman ısıl işlem sonrasında mikro çatlaklar oluşuyor. İlk etapta bunlar fark edilmesi zor zararlar. Belli bir süre sonra oluşan bu çatlaklarda kırılma yaşıyorsunuz. Fakat MILLUTENSIL alıştırma presi sayesinde, bu parçaların çok daha sağlıklı şekilde alıştırmasını sağlıyorsunuz. Dolayısıyla kalıp ömrü yüzde yüz etkileniyor.
Aynı zamanda, alıştırma presi sayesinde yüzeyleri tamamen birbirine değdirmiş oluyorsunuz. Enjeksiyonda da zaten esneme olmadığı için, bir yerlere zarar vermemiş oluyorsunuz ki alıştırma presinin asıl avantajı da burada ortaya çıkıyor. Kaldı ki bir kalıbın düzlemsel olmaması, enjeksiyon tezgahının kolonlarının dengesiz çalışmasına sebep olur ve tezgahın ömründen çalar. Alıştırma presi sayesinde kalıbın düzlemselliğini de kontrol edebildiğimiz için, enjeksiyon tezgahlarımızı da koruma altına almış oluyoruz.
Eğer kalıp yüzeyleri çok formluysa, alıştırma bitikten sonra her iki yüzeyin de fotoğrafını alıyoruz. Bu sayede müşteriye, “Kalıp alıştırma presine bağlandı ve mavi boya kontrol edildi” diyebiliyoruz. Böylece müşteri, şundan emin olabiliyor; mesela bazen enjeksiyonda kalıp tonajı yanlış seçilebiliyor. 500 tondan bağlanarak baskı alıyor ve tonajı yeterli olmadığı için bir miktar açıyor. Siz bunun alıştırmadan mı yoksa enjeksiyon tonajı yetmedi, kalıp açtı çapak yaptı bunu tespit etmek bazen sıkıntı olabiliyor. Çünkü enjeksiyon tarafı, yani üreten taraf diyor ki “Benim tezgahım yepyeni, benden kaynaklı bir sıkıntı yok. Parçayı bastım, kalıpsa sorun var” ama biz bu boyayı gösterip, sonra da bazen kompratör koyuyoruz enjeksiyon tezgahında ve açtığını görüyoruz. İşte alıştırma presinin böyle bir avantajı var. Siz şayet mavi boyayı ince sürüp, karşı tarafında da o boyayı görebiliyorsanız ve enjeksiyonda 500-600 ton kullanıyorsanız, -ki bizim alıştırma presimizin maksimum tonajı belli, 150bar yani 150 ton diyoruz- hiçbir zaman 500 tonu kullanamıyoruz, dolayısıyla biz bunu burda denedik ve boyayı gördük dediğimiz anda tartışma sürecini de sonlandırmış oluyoruz. Çünkü alıştırma presi elinize bir kanıt sunmuş oluyor.
Çekiçleme konusu, alıştırma presinin avantajlarının ön plana çıktığı bir diğer nokta. Mesela siz bir kalıbı yaptınız, ilk denemesini yaptınız. İkinci ve üçüncü denemelerini de yaptınız. Ancak kalıbın belli bir süre, 1000 veya 2000 sefer mamul basılmadan kapatılıp açılması gerekiyor. Müşterilerimizin bizden, alıştırma yüzeylerinin birbirlerine değmesi yönünde talepleri var. Hatta sırf bu sebeple, receiving plate dediğimiz karşılama plakaları konulur. Plakanın olduğu noktaya gelince, kalıp alışmış olur. Alıştırma presindeki çekiçleme bu süreci hızlandırıyor. Bazen plastik desenleri üzerinde bir takım istenmeyen çizikler oluşur. İşte alıştırma presindeki çekiçleme sayesinde, kalıp yüzeyleri birbirine iyice alıştığı için, bu istenmeyen durum ortadan kalkar. Sizin aslında enjeksiyon makinesinde bin seferde yaptığınız şeyi, alıştırma presi hızlı bir şekilde yapar.
Genelde insanların tezgahın tonajıyla alakalı düşünceleri, sizin söylediğinizin tam tersi şeklinde. Yani alıştırma presinin tonajının, enjeksiyon makinesinin tonajına yakın olması gerektiği gibi bir algı var. Bu sayede de yüksek tonajda oluşabilecek olan yüzey deformasyonun önüne geçmiş oluyorsunuz aslında?
Kesinlikle! Örneğin, 800 tonluk enjeksiyon makinesinde denenen bir kalıbı ele alalım… Siz bu kalıbı alıştırma presinde 30-40 barla alıştırdıysanız, enjeksiyon makinanız 800 tonunu enjeksiyon yapmak, ütülemek ve parçayı düzgün almak için kullanacaktır. Ama alıştırma presi kullanmazsanız, o zaman 200-300 tonunu kapamayı gerçekleştirmek için kullanacak ve kalan tonajı parça basımına kullanacaktır. Yani siz aslında alıştırma presinde, enjeksiyon makinasının parça basımında kullanması gereken tonajı kullanmış oluyorsunuz. Bahsettiğiniz şey aslında tamamen bununla ilgili.
Biz MILLUTENSIL’i almadan önce şunu söylüyorduk; arkadaşlar kalıbı enjeksiyona bağlıyorlar, boyayı gösteriyorlar, sonuç süper ama parça basmaya geçtiğimizde bir sürü çapak gördük. Bu da şundan kaynaklandı; biz makinanın kapama kuvvetinin çok büyük bir bölümünü sıkmak için kullandık. 100 veya 200 tonluk bölümünü ise enjeksiyon için kullandık ve dolayısıyla yetmedi. İşte alıştırma presinde en büyük kazanımımız bu oldu. Yani enjeksiyon makinasının tüm basıncını kalıbı kapatmak için değil, enjeksiyon için kullanabiliyoruz.
Türk kalıp sektöründe yaşanan gelişmeleri nasıl değerlendiriyorsunuz?
Evet, Türk kalıp sektöründe ciddi sıçramalar, gelişmeler olduğu kesinlikle doğru. Özellikle son yıllarda Avrupa’dan da büyük ilgi var Türk kalıpçılarına. Avrupa’dan geçtiğimiz aylarda bir çok firma geldi, keza bu önümüzdeki yaz aylarında da yeni firmalar gelecekler, zira Avrupalı firmalar Türk kalıpçılarına çok ciddi bir ilgi duyuyorlar. Bunun sebepleri arasında yapılan işin kalitesi ve termin uyumluluğu ön plana çıkıyor. UKUB’un da katkısı var bu olayda. Derneğin iki yıl önce yaptığı çalışmaların meyvesini biz yedik. Nasıl diye soracak olursanız; bir kere Türk otomotiv firmalarına, Türk kalıpçılığını çok iyi tanıttılar. Bildiğiniz üzere Renault ve Ford marka araçların bir çoğunun kalıpları Türkiye’de başarıyla yapıldı. Bu sebeple de kalıpçıların kendilerine olan güveni arttı. Oluşan bu güven artışına bağlı olarak yeni yatırımlar ve yurt dışına açılma cesareti daha fazla oldu. Yurt dışından da bu tepkiyi alıyoruz. Sürekli yeni firmalar, müşteriler gelmek ve incelemek istiyorlar ve umarız daha iyi olacak.
Eskiden Renault ve Tofaş kalıpları Türkiye’de yaptırıp, satın almayı yurt dışından yapıyordu. Bu durum artık ortadan kalktı değil mi?
Evet, bu konuda da Clio ve Transit projeleri birer kırılma noktası oldular. Çünkü bu projelerin Türkiye’de üretilmesine kadar verildiği zaman, kalıpçılığın önünde de çok büyük bir fırsat doğdu. Ki bu konuda da tüm kalıpçılar adına rahatlıkla söyleyebilirim ki oldukça başarılı olduk. Ve bu başarı neticesinde de Türkiye’de kalıpçılar yaptı, üreticiler de üretiyorlar ve araçlar şu anda sıkıntısız şekilde yolarda geziyorlar. Bu da yeni dönemde OEM firmalarının Türkiye’de kalıpçılara talep akışı olmasını sağladı. Mesela Volkswagen, Mercedes, BMW, Porsche gibi ana üretici firmalar, yeni ve devam eden projeleri için Türkiye’ye bakıyorlar. Ama Transit ve Clio öncesin kafalarda soru işaretleri vardı. Şu anda bizlerden sürekli teklif istiyorlar. Artık güvensizlik algısını kırdık, çünkü yapılan işlerin başarıları ortada. Şu anda fiyat konusunda, diğer ülkelerle karşılaştırma yapıyorlar. Bu konuda da avantajlı olduğumuzu düşünüyorum. Asya firmalarına kıyasla iletişim, dil, kültürel ve lojistik anlamda çok büyük artılarımız bulunuyor.